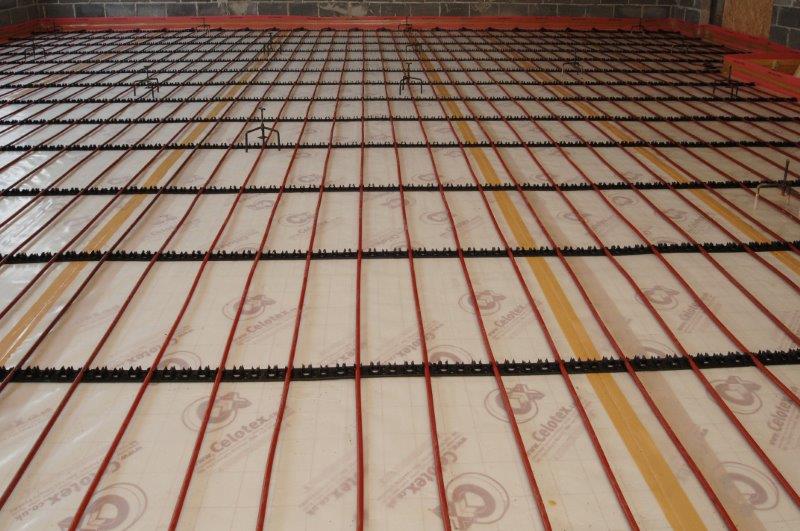
About Insulation
Let us take a look back in time when insulation became an element of the building process.
Insulation was introduced into the construction of dwellings over many years. Firstly, loft insulation followed
by cavity wall insulation and then floor insulation.
The purpose was to conserve energy consumption and reduce carbon footprint.
As more and more insulation elements were added to the build process more issues arose, an example the formation of mould and condensation as a
direct result of improvements to Part L and Part C. The issues categorised as interstitial condensation with numerous studies carried out by University College London, Leeds Metropolitan University and Department for Communities and Local Government.
The studies identified areas of concern within the study of interstitial condensation. At site level there lacked practical
understanding of the need for vapour control layers as this is a key component in the correct installation of the floor insulation.
A VCL sometimes is referred to as a DPM, and whilst the material has similar properties of 1000 gauge polythene a DPM arrives on site multi folded. When opened out and used as a VCL the creases can result in induced cracking of the screed layer. A true VCL is single wound with a cardboard core.
Over the years insulation in the roofs, walls and floors has been upgraded to improve the U valve and the heat loss. At one time there was no insulation present in domestic dwellings. In the days of Parkray and Rayburn coal fired boilers insulation was not a requirement or necessity. Solid fuel burned all day and produced constant heat. As a consequence the domestic hot water would boil over and the need to draw off hot water to cool the cylinder. Insulation undoubtedly will have compounded this. With the introduction of gas and oil fired boilers came the ability for greater levels of electrical control in the form of timers, room and cylinder thermostats. This brought to the forefront the benefit for energy conservation. Lofts were the initial space for insulation to prevent heat loss through the roof structure. The first encounter of loft insulation was the irritating mineral wool laid at 25mm.
In the mid 80’s was the start of cavity wall insulation and this aspect of insulation were assigned to bricklayers. Needless to say this did not bode well with
the “brickies”. On to the 90’s, in the early 90’s a change in the building regulations required the ground floors be insulated to save energy. Floors are classified as:-
· Ground floors, in contact directly or indirectly with the ground
· Exposed floors, forming the lowest part of a structure over unenclosed airspace, for example a balcony or car port
· Intermediate floors, having heated space above and below
Ground floors are defined as a structure that bears its weight on the ground floor or suspended i.e beam and block. The significance of this in respect of
underfloor heating is the heat loss which will be lost into the ground by absorption. Damp, moist ground has a greater degree of absorption than dry ground.
Particular attention has to be given to edge insulation to prevent heat loss and cold bridging. Not forgetting the ever important VCL layer.
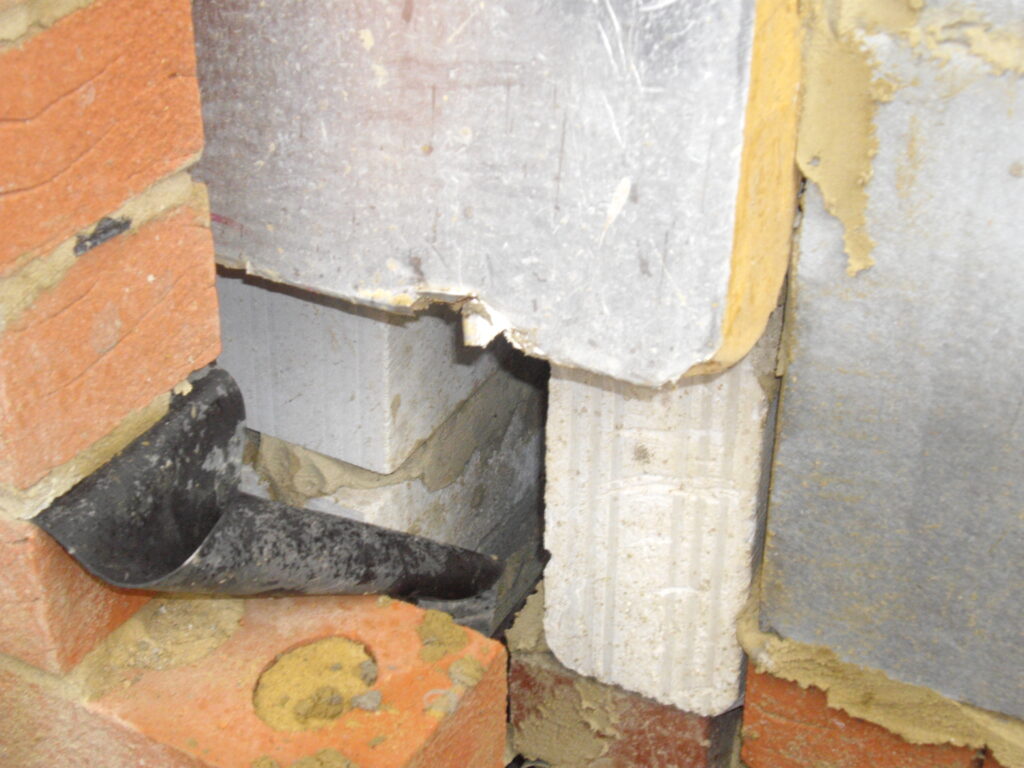
The junctions between the floor and wall structures if not completed correctly will inevitably result in heat loss and increased running costs.
The cavity wall insulation should extend 150mm to 200mm below floor slab creating an overlap of insulation between these two elements of the build
construction. Failure in observing this crucial practise will result in high levels of heat loss. SAPS calculations are undertaken to determine the minimum thickness of insulation materials with approval of building control. SAPS calculations indicate the product and thickness required. It is recommended that you adhere to what is specified in the SAPS. Beware the local merchants are often heard to say the brand does not matter as it all the same stuff and this is certainly not true!
Thermotech operates a repair and report service on the shortfalls in the performance of underfloor heating installations already in use. A frequent question we are asked “Why does my property never seem to get warm?”
Our response is there are many reasons why but as we are talking about insulation this is one aspect of an underfloor heating system which cannot be rectified short of digging up the floor and starting again. We have established the lack of insulation, insulation not to specification, by core drilling a series of holes in the floor structure and exposing the insulation.
Thermotech was engaged to undertake the complete installation of underfloor heating system and pumped liquid screed on a prestigious build for a private client. With a build that would push the boundaries in concrete construction. Large cantilever canopies were part of the intermediate floor construction. The exposed canopies posed a concern due to the fact the canopies would be exposed to the external air temperature and could result in heat loss through the cast concrete floor slabs.
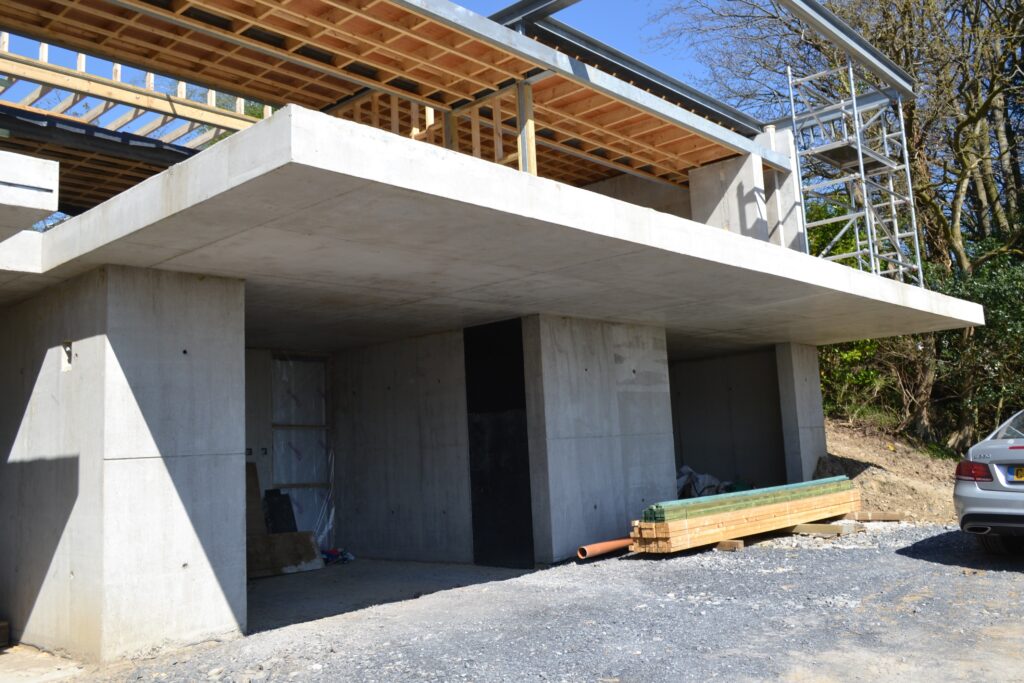
This fact was not a consideration until Thermotech were engaged in dialogue with the client, the contractors and professional advisor.
A remedy was proposed by Thermotech resulting in an amended specification and plans. The problem solved you may now think, alas no. When Thermotech undertake the complete underfloor heating and screed installation is carried out and prior to commencement of works a laser survey is undertaken. Having overcome the theoretical issues with overhanging canopies and the likelihood of heat loss, the laser survey established the large glass panoramic bi-folding sliding and fixed panel glass doors were 35mm out of level across the total length of some 60 linear metres.
What does this mean? If Thermotech followed the datum supplied the panoramic bi-folding glass doors would not open as the finished floor level was
above the height of the door threshold. Once again we addressed this with the client. Our view to remedy was simplistic; the removal of doors and glass panels and reset to level as sufficient gaps were available above. The remedy was dismissed as no-one would agree on liability.
A suggestion put forward by one of the parties was to reduce the screed depth. Needless to say they had no knowledge of British Standards, the application of screeds and the ongoing problems which may occur. It was back to the drawing board and further amendments to the floor detail to encompass the higher value insulation product. A costly delay as a result of the lack of communication; one of the key elements to a successfully run site is communication, communication and even more communication.
Site project managers are responsible in explaining the detail of specific jobs and the co-ordination of these. When explaining to a site operative the
requirements of him or her, the project manager should request the explanation is repeated back in order to eliminate confusion. Often it can be a misunderstanding of interpretation that results in an error.
Example a decorator was asked to paint a wall with black and white stripes. As a result of a misinterpretation the wall was painted with white and black stripes.