Complete Installations
Take a look at what we do prior to attendance at site.
In our workshop we build our manifolds prior to attendance at site. This procedure saves between two and three days allowing us to completely build the manifold assembly including pump mixing valve, wiring centre, micro centre, manifold temperature controller and relay.
Below is a sequence of images depicting the build-up and assembly of our manifolds, with each image outlining the individual components and the functionality. Do not be fooled when other companies say we completely install your underfloor heating when in fact what they mean is they bolt the manifold in position and pipe to and from it. (see the instructions left by another company!)
It all starts with a manifold back panel with a 20mm off stand to allow for rear cable entry.
Manifold back panel is assembled with commercial quality fixing rail system.
Attached to fixing rail system are rubber insulated pipe supports, rubber insulated pipe supports for a secure fixing and to minimise vibration and sound
The manifold is assembled onto the back panel. The manifold is complete with isolating valves
The mixing and temperature blending valves along with pump valves and secondary Pegler isolation valves and 22mm copper pipework are secured onto back panel. Other OME’s use fabricated pipework that has resulted in pipework failure. We always use 22mm copper pipework and never returned to change a complete manifold. Our mixing and blending valves are industry standard products and are backward compatible for over thirty years.
A dedicated underfloor heating pump is installed
Wiring and Micro centre mounted onto back panel ready for electrical assembly
Internal wiring loom assembly depicting the manifold temperature controller. We only use a digital controller for control of the blending and mixing valves thus achieving finite accuracy. Included as standard is a relay to prevent electrical feedback. With modern heating systems there can be many connections from different heat sources i.e. heat generator, heat pumps and solar panels. Where these are common together there can be the possibility of electric feedback i.e. one system switching on a circuit that is not programmed to run and this is generally referred to as reverse energising. We include a relay as a standard component in our systems, preventing the possibility of reverse energising.
In-situ manifold assembly complete with fitted actuators, blending valve, circulating pump, micro centre and digital controller. Actuators for individual rooms labelled up; hydrostatic test complete along with temporary electrical supply allowing us to demonstrate the manifold is fully operational. (link to super insulation).
The observant amongst us will note the secondary pipework is not connected to the heat source however the system is recording a floor temperature of 18.3C. The underfloor heating system was tested prior to the screed laying and a large part of this floor was exposed to solar gain through bi-fold glass doors.
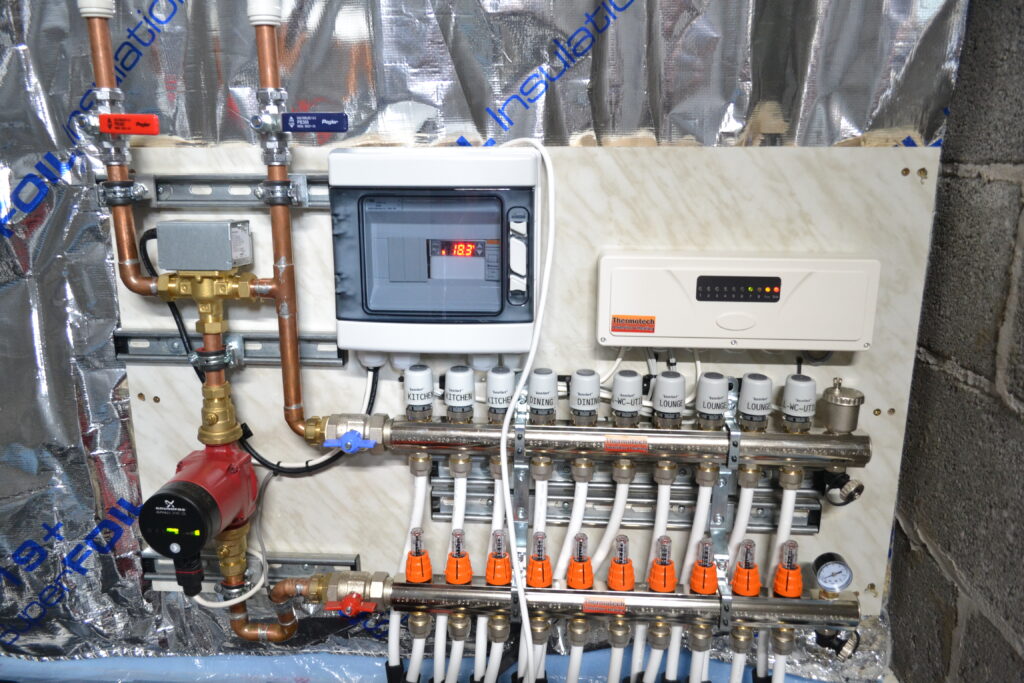